Mastering the Art of Forming Mould: A Comprehensive Guide
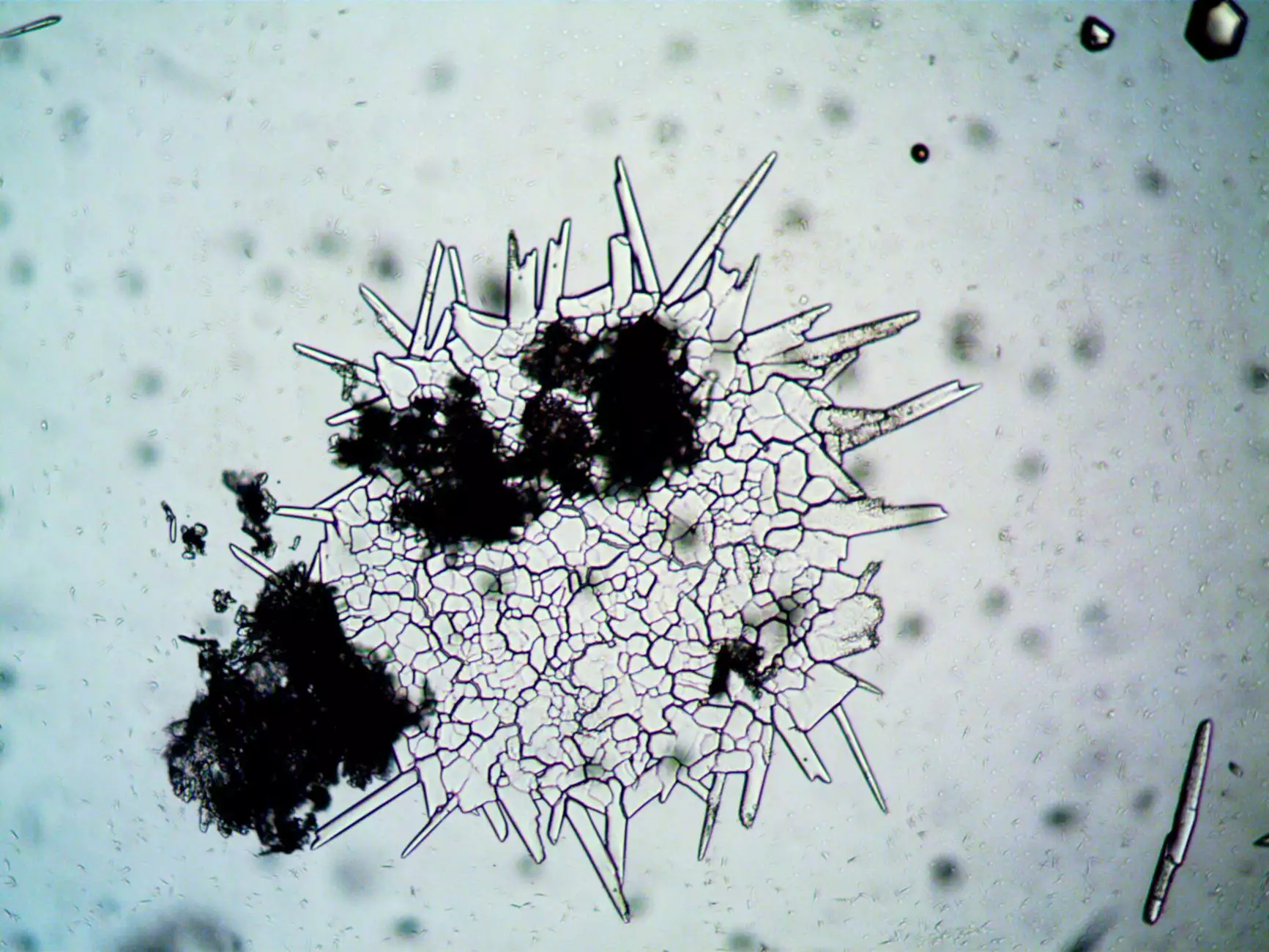
Introduction to Forming Mould
Forming mould techniques are essential in various industries, ranging from art supplies to product design and 3D printing. In this guide, we will explore the intricacies of forming mould, its applications, and tips for achieving mastery in this essential skill.
What is Forming Mould?
The term forming mould refers to the process of shaping materials to achieve a desired form. This can involve various techniques, including casting, injection moulding, and vacuum forming. Each method serves a specific purpose and is chosen based on the material being used and the final product's requirements.
Applications of Forming Mould in Different Industries
Understanding where and how forming mould techniques are applied can inspire creativity and innovation in your projects. Here are some significant applications:
- Art Supplies: Artists often utilize moulds to create unique sculptures and designs. Moulds allow for intricate details that are otherwise challenging to achieve by hand.
- Product Design: In product development, forming moulds are crucial for prototyping and manufacturing. They ensure consistency and precision in produced items.
- 3D Printing: Advanced technologies in 3D printing often incorporate forming mould techniques, enabling the creation of complex structures and parts.
Types of Forming Mould Techniques
There are various forming mould techniques, each with its benefits and specific use cases. Here are some of the most common methods:
Casting
Casting involves pouring a liquid material into a mould and allowing it to harden. This technique is ideal for creating intricate designs and is widely used in the production of sculptures, as well as in industry for producing metal parts.
Injection Moulding
Injection moulding is a process used predominantly in manufacturing plastic items. The plastic is melted and injected into a mould, where it cools and hardens into the final product. This method is efficient for mass production.
Vacuum Forming
Vacuum forming uses heat to soften a thermoplastic sheet, which is then placed over a mould. A vacuum is applied, pulling the plastic tightly against the mould. This technique is commonly used for packaging and creating light-weight structures.
Choosing the Right Mould for Your Project
Choosing an appropriate mould type is crucial for the success of your project. Here are some factors to consider:
- Material: The choice of material for your mould will affect the outcome significantly. Consider its durability, flexibility, and heat resistance.
- Complexity of Design: Intricate designs may require more advanced moulding techniques, such as injection moulding.
- Volume of Production: For high-volume production, efficiency is key. Techniques like injection moulding would be more appropriate.
Best Practices for Working with Forming Moulds
To achieve high-quality results with your forming mould projects, follow these best practices:
Preparation
Proper preparation is vital. Clean your moulds thoroughly and ensure they are free from any debris that could affect the final product.
Material Selection
Your choice of material can impact both the quality and durability of your mould. Always opt for high-quality materials to ensure lasting results.
Temperature Control
Temperature plays a crucial role in the forming process. Regularly monitor and control the temperature of the material to prevent warping or defects.
Testing and Prototyping
Before committing to a final design, create prototypes to test how the mould performs. This step can save time and resources in the long run.
Adopting 3D Printing in Forming Mould Techniques
The advent of 3D printing has revolutionized the forming mould landscape. By enabling rapid prototyping and design flexibility, 3D printing can significantly enhance your workflow:
Speed and Efficiency
3D printing streamlines the process by allowing quick alterations to designs. You can instantly produce and iterate on mould designs without the need for extensive tooling.
Complex Geometry
With 3D printing, it is possible to create moulds with complex geometries that would be challenging and costly with traditional methods. This capability opens up new possibilities for creativity in design.
Cost-Effectiveness
For small runs and prototypes, 3D printing can be more cost-effective compared to traditional moulding options, as it eliminates the need for expensive moulds.
Future Trends in Forming Mould and 3D Printing
The future of forming mould technologies is bright, with innovations continuing to emerge. Look out for:
- Biodegradable Materials: As sustainability becomes a priority, the use of eco-friendly materials in forming mould applications is on the rise.
- Smart Moulding Techniques: Integrating technology such as sensors in moulds for real-time monitoring can improve quality control and efficiency.
- Hybrid Manufacturing: Combining traditional moulding techniques with 3D printing is expected to become more prevalent, allowing for versatile production methods.
Conclusion: Elevate Your Projects with Expert Forming Mould Techniques
Mastering the art of forming mould is crucial for success in art supplies, product design, and 3D printing. By understanding the various techniques, selecting the right materials, and adopting best practices, you can elevate your projects to new heights. Embrace innovation and stay informed about trends to keep your skills sharp and relevant in this ever-evolving landscape.
Resources for Further Learning
To deep dive into forming mould, consider exploring various resources:
- Online courses in product design and mould making.
- Workshops on 3D printing technology.
- Books on advanced moulding techniques and materials.